La capacità creativa italiana è sempre stata apprezzata in tutto il mondo e anche nei momenti di crisi riesce a dare il meglio di sé, unita a quello spirito di generosa dedizione che anche le imprese sanno dimostrare.
In questo periodo caratterizzato dall’emergenza coronavirus, a Brescia, due imprese stanno producendo respiratori artificiali con una tecnica innovativa: la stampa 3D. Si tratta di un metodo già usato per la fabbricazione di dispositivi medici, ma non ancora applicato per strumenti appositi contro il virus.
Le due aziende in questione sono Isinnova, presieduta dall’ingegner Cristian Fracassi e che si occupa di ricerca e sviluppo in ambito medico, e Beretta, storica armeria. Insieme stanno sviluppando una soluzione innovativa e sostenibile in grado di offrire assistenza ai malati, trasformando una maschera snorkeling di Decathlon in un respiratore. Due mondi diversi che però in questo momento di emergenza si sono uniti per dare una mano ai medici e agli infermieri in difficoltà.
L’idea di modificare una maschera subacquea in un respiratore è venuta a Renato Favero, ex primario dell’ospedale di Gardone Valtrompia, il quale, avendone una in casa, ha provato a smontarla e a studiarne nuovi usi. Così, ha scoperto che modificando una valvola e costruendo un raccordo per il boccaglio è possibile ottenere un respiratore. Successivamente ha proposto la sua idea a Issinova e, insieme, hanno messo a punto un sistema di respirazione artificiale.
Le maschere prodotte sono di tipo Cpap (Continuous Positive Airway Pressure, in italiano “pressione positiva continua delle vie aeree”), in grado di salvare la vita a chi si trova in terapia intensiva.
Il prototipo è stato testato all’Ospedale di Chiari e si è dimostrato correttamente funzionante. La valvola, che rappresenta la parte fondamentale del respiratore è stata battezzata Charlotte. C’è da dire che né la maschera né il raccordo valvolare sono certificati e il loro impiego è vincolato a una situazione di assoluta necessità. L’uso da parte del paziente è subordinato all’accettazione dell’utilizzo di un dispositivo biomedicale non certificato, tramite dichiarazione firmata.
Al fianco di Issinova, come detto, si è schierata Beretta, che per l’occasione ha riaperto il dipartimento di proto riparazione chiuso dopo l’entrata in vigore del DPCM che ha fermato le imprese non essenziali. Oggi però, anziché produrre armi, Beretta realizza le valvole Charlotte con la stampa 3D.
L’intera azienda si è data subito da fare e, in pochi giorni, ha stampato più di 50 valvole e dispone di materiale a sufficienza per produrne altre 500. La scorsa settimana il presidente di Beretta, Franco Gussalli Beretta, ha lanciato un appello su Linkedin per recuperare il composito specifico DuraForm HST (SLS) 3D necessario per costruire ancorapiù valvole. All’appello ha risposto Prototopi, azienda di Reggio Emilia, che sta inviando a Brescia 150 kg di polvere.
Oltre a Beretta al progetto collaborano altre 15 imprese. Inoltre, Issinova e Beretta hanno avuto subito l’aiuto di Decathlon che ha messo a disposizione i suoi disegni tecnici e diversi lotti di maschere pronte per la modifica. L’iniziativa non ha scopo di lucro, le maschere vengono regalate agli ospedali e Issnova non percepisce diritti sull’idea del raccordo.
Nel giro di poco tempo l’invenzione made in Italy ha avuto grande risalto internazionale, tanto che stanno arrivando richieste anche dagli Emirati Arabi e da paesi dell’Est Europa.
Se, quindi, fino a ora, l’Italia ha mostrato al mondo il volto dell’inefficienza politica e del ritardo nella dotazione di mezzi – con i tragici effetti sotto ai nostri occhi – con questa invenzione ha dimostrato ancora una volta di essere in grado di “inventarsi” soluzioni innovative.
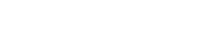